Research
Current Research:
Materials Compatibility with PbLi Eutectic for Fusion Blankets
The group is constructing a molten PbLi loop to investigate corrosion of blanket facing materials for fusion reactors.
Solid State Processing of Bulk Metallic Glasses with increased Tg
Bulk Metallic Glasses (BMGs) are metals without crystal structure (amorphous). These materials are traditionally manufactured by rapid quenching (cooling rates of >1000 °C/s) of molten alloys. Solid state processing offers the advantage of broadening the available alloy compositions that can be formed into fully bulk amorphous structures. Most investigated BMGs have relatively low glass transition temperatures (Tg). Solid state processing may allow for the increased use of refractory metals in these alloys, which will increase the glass transition temperature, allowing these materials to be used in higher temperature enviornments, including nuclear reactors. Some BMGs have been show to have increased corrosion resistance and radiation damage resistance.
Additive Manufacturing of High Entropy Alloys (HEA) and Medium Entropy Alloys (MEA) using Elemental Powders
High and Medium Entropy Alloys are a class of advanced alloys of interest in nuclear systesm. By manufacturing them by using Laser Directed Energy Deposition Additive Manufacturing (L-DED AM), starting with elemental powder feedstock, we hope to demonstrate these specimens exhibit properties comprobable to tradional manufacturing.
Development of Advanced High-Cr Ferritic/Martensitic Steels
To meet the requirements of next-generation nuclear reactors, materials must be developed that can withstand irradiation doses up to 600 displacements per atom (dpa). Ferritic/Martensitic (F/M) steels are a promising class of iron (Fe) based alloys, containing chromium (Cr) levels of 9-12 % by weight, that have huge potential to meet the ambitious requirements for next-generation reactors. F/M alloy HT-9 has had great success in reactor applications because it offers excellent resistance to irradiation hardening, swelling, and embrittlement at reactor service temperatures (400-600°C), and also has outstanding thermal conductivity and corrosion resistance. The primary impediment for widespread industrial implementation of HT-9 is the development of embrittlement at slightly lower temperatures (300-400°C) that occur at the inlet regions of reactors. Read more...
Multilayer ARB processed Ni/Ta, Cu/Nb, Cu/Zr
The team has investigated the physical properties of ARB processed composites of Ni/Ta, Cu/Nb, Cu/Zr, and characterized the thermal and electrical conductivity of Cu/Nb specimens. This work investigated the trade of between the increased radiation damage resistance and mechanical properties and the decreased conductivity as it pertains to composite layer thickness.
Nondestructive Investigation of Physical Properties of Actinide/Lanthanide Surrogate Materials
Nondestructive investigations are of interest for working with small quantities of material. This work is investigating what tools can be developed to investigate rare actinide and lanthanide materials where the use of small quantities of material is common.
Remote High Temperature Mechaincal Testing of Activated Specimens
The Lobo Hot Cell has been outfitted with a Zwick Roell tensile test machine. This capability allows for fully remote mechanical testing at room temperature up to 900 °C of irradiated specimens. Current work is on extending this capability to cryogenic temperatures for non-activated specimens.
Completed Research Projects:
Joining Studies of ODS and FeCrAl Steel Alloys
FeCrAl and ODS steels are excellent candidates for advanced reactor designs due to their strength at elevated temperatures and resistance to radiation damage. However, these alloys are also known for the formation of defects during welding. Porosity, cracking, and lack of fusion lead to weak joints susceptible to failure. Experiments on the effects of pre-weld and post-weld heat treatments on the quality of similar and dissimilar joints are being performed. Corrosion testing in flowing molten lead of both joined and parent metals are being performed using the Lobo Lead Loop. The changes in mechanical and microstructural properties due to welding and corrosion are being analyzed using micro-indentation and nano-indentation hardness testing, room and elevated temperature tensile testing, optical and scanning electron microscopy, and energy dispersive spectroscopy.
Nanostructured Composite Alloys for Extreme Environments
The objective of this proposal is to develop extreme performance nanocomposite alloys with engineered interfaces that can withstand irradiation doses up to 600 dpa at elevated temperatures (up to 700°C) for demanding nuclear environments such as fast reactor cladding applications. Read more...
Microstructure-mechanical property correlations in additively manufactured AISI 420 martensitic stainless steels
Additive manufacturing (AM) is a promising way to produce metallic parts with complex geometries and functional structures for applications in the automotive, aerospace, and medical industries. Low-carbon martensitic stainless steels have been used in steam turbine blades, hydraulic turbines, pumps, and high-pressure pipes in the energy and petrochemical industries. AISI 420 martensitic stainless steels (0.4%C, 12.7%Cr, in wt.%) were successfully deposited near-fully dense onto 316L substrate by Laser Engineered Net Shaping (LENS®) process. The cross-sectional examination by electron microscopy and XRD confirms the dual-phase microstructure of martensitic needles and austenite. Preliminary mechanical characterization by micro-Vickers hardness tests shows a uniform hardness trend across the build. Microstructure, the chemical composition of the phases, the mechanical properties, and corrosion resistance of the steel could be affected by the heat treatment which is very sensitive. The team investigates to optimize the heat-treating method to improve its mechanical properties.
Microstructure-mechanical characteristics in Ti/TiC composites fabricated by laser-directed energy deposition
1 M Radhakrishnan et al., Microstructural evolution in Ti/TiC composites fabricated by laser-directed energy deposition, Additive Manufacturing.
Ceramic particle reinforced metal matrix composites (MMC) are promising materials for many industrial applications due to their favorable combination of properties. Titanium carbide (TiC) is a common ceramic reinforcement for Ti-based MMCs that provides improved stiffness, hardness and wear properties while retaining relatively lower density. In this work, microstructure evolution in laser deposited monolithic titanium/titanium carbide (Ti/TiC) composites with 20, 40 and 60 vol.% of TiC powders was investigated. Microstructure evolution and build quality in monolithic deposits were compared with a gradient Ti/TiC composite with composition ranging between 20 and 60% TiC. The bulk relative densities exceeding 99% were achieved in the deposits. The evolution of microstructures and local chemical compositions in the deposits under rapid melting and solidification were systematically analyzed using X-ray diffraction, electron probe micro-analyzer and scanning electron microscopy. Assessment of mechanical integrity of the deposits involved microhardness, tensile testing and fractography. One of the major conclusions from the present work is that the quality of the TiC powder used in the starting feedstock, i.e. the extent of pre-existing cracks, played a key role in the mechanical integrity of the deposits. This observation suggests that the mechanical performance of the Ti/TiC composite deposits could be improved with the reduction of undissolved TiC content in the deposit. Use of a lower volume fraction of smaller particles together with tailored processing parameters that promote complete dissolution of the TiC will eliminate issues associated with pre-existing cracks and stress concentrations with large, pointed particles.
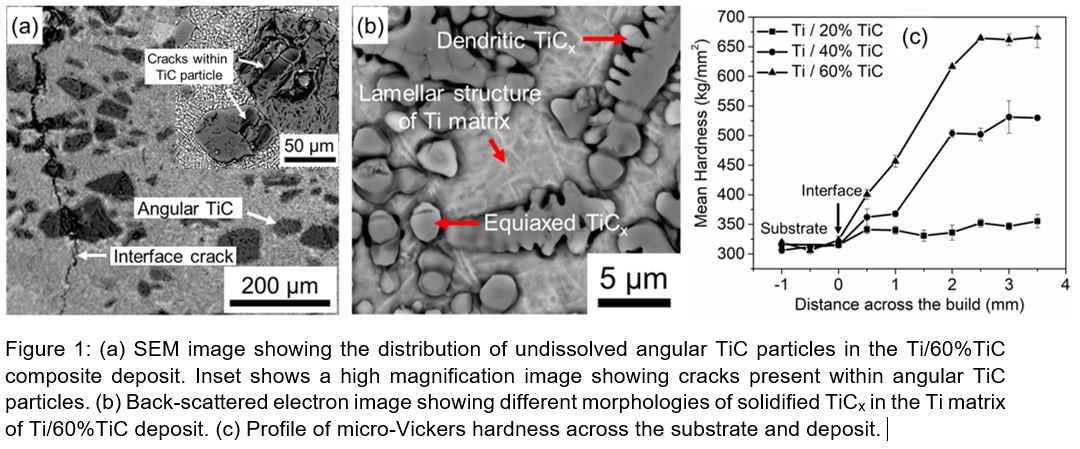
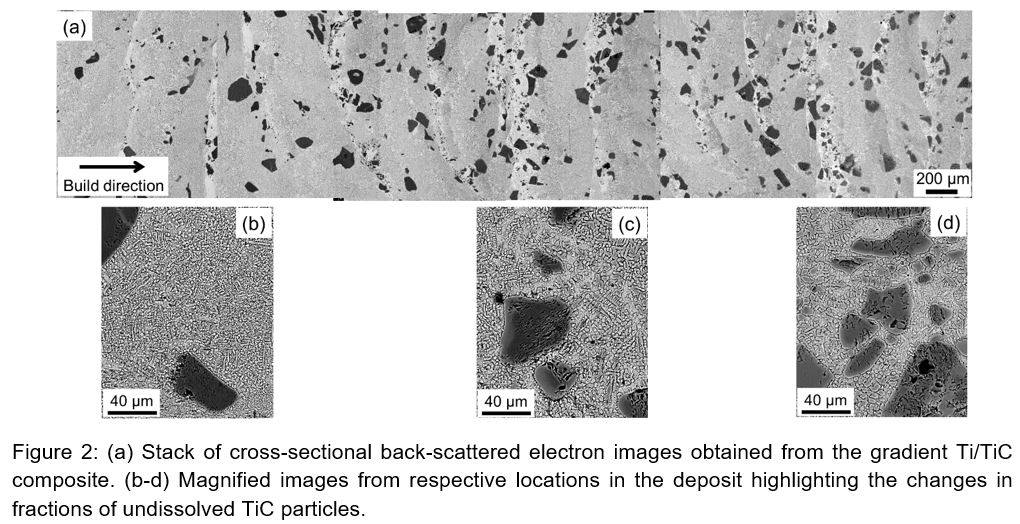
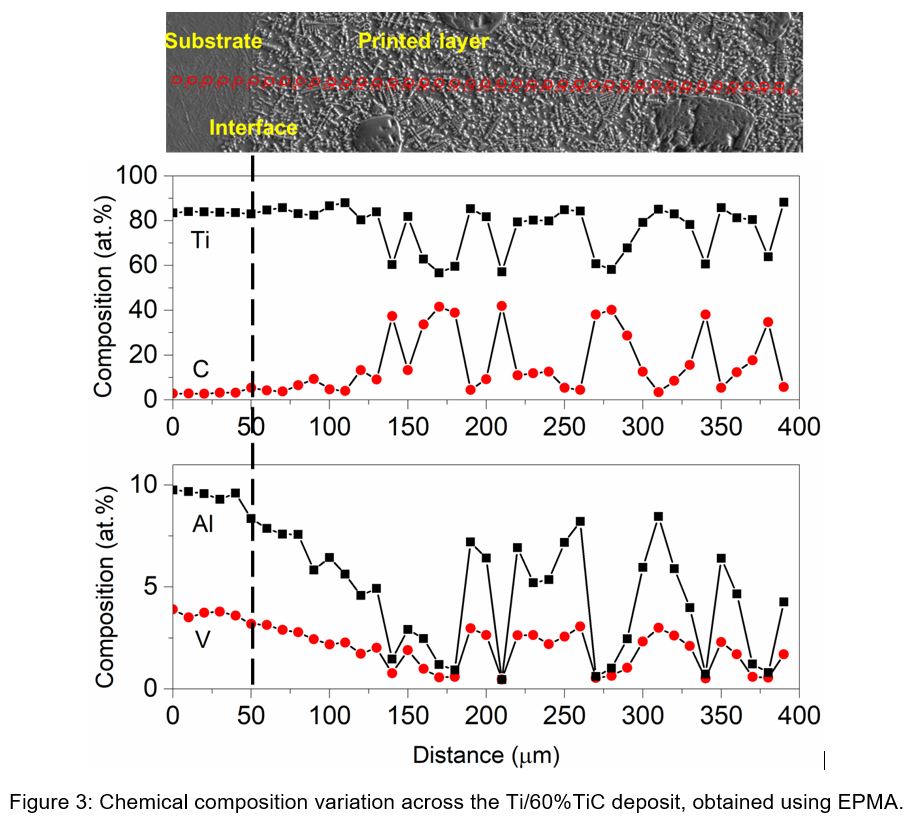
Electrically-Assisted Tubing Processes for Enhancing Manufacturability of Oxide Dispersion Strengthened Structural Materials for Nuclear Reactor Application
Stress vs. plastic strain of 14YWT at various temperatures: Solid lines are obtained from specimens tested under furnace heating while the dashed lines are for specimens tested joule heating due to passage of electrical current, also called electrically assisted (EA) deformation. Significant improvement in deformability is observed after EA testing at similar temperatures.
(a) Focused Ion Beam (FIB) image of grain morphology. Uneven distribution of grains exists even before EA deformation presumably due to rather complex processing steps. (b) A high-resolution Transmission Electron Microscopy (TEM) image of the fine-scale precipitates exists even after deformation at high electrical currents showing the stability of the oxides as well as the initial success of EA deformation.